Circular 670
Thomas Jenkins
College of Agricultural, Consumer and Environmental Sciences and College of Engineering, New Mexico State University
Author: Professor, Department of Engineering Technology and Surveying Engineering, tjenkins@nmsu.edu, New Mexico State University. (Print friendly PDF)
Introduction
In many parts of the world, including New Mexico (NM), water and energy availability are growing concerns. In areas where connection to an electric utility is not available, the primary technologies for water access—surface sources or pumping—have remained fairly constant for decades. As demands for higher quantities and quality of water, lower costs, improved reliability, and environmental concerns have increased, many livestock and agricultural producers are investigating an alternative technology for remote water pumping: direct-coupled solar photovoltaic (PV) powered systems.
Since the process to design and implement such a system may be a challenging task, New Mexico State University's Engineering NM program initiated a project to provide the Cooperative Extension Service (CES) with a demonstration module, an interactive design spreadsheet, and literature related to solar water pumping to better inform NM water users about the benefits and methodology of implementing this technology. Available through NMSU multimedia and the CES statewide Extension agent network, these tools serve to educate interested constituencies (primarily farmers and ranchers) in using solar energy to pump water.
This publication provides a general discussion of how to design a photovoltaic-powered solar water pumping system for livestock. A companion publication, Circular 671, Designing Solar Water Pumping Systems for Livestock: User Manual (https://pubs.nmsu.edu/_circulars/CR671.pdf), provides step-by-step instructions for using a Microsoft Excel spreadsheet to perform necessary calculations for designing a solar pumping system.
Surface Water Sources and Livestock
Livestock, crops, and people often depend upon surface sources of water (streams, ponds, catch tanks, etc.) or wells accessing underground aquifers1. Because of a variety of benefits, and increased regulations in some states, it is often desirable to move water from a surface source to a different location, elevation, or “drinker,” or to pump water from a remotely located well.
For surface sources, a well-vegetated riparian zone establishes a buffer that filters and purifies water as it moves across the zone, reducing sediment loads, supporting soil stability, improving water quality, and enhancing wildlife habitat. Excessive livestock pressure on surface sources often causes nutrient loading, streamside vegetation damage, erosion, pollution, and decreased animal growth and health. One approach is to remove or limit access to these areas; however, often this is the only viable water source for producers. Fortunately, research shows that in many cases pumping water to a different location, combined with a managed rotational grazing plan 2, optimizes animal performance, pasture use, water quality, and wildlife in these zones (Buschermohle and Burns, n.d.; Morris and Lynne, 2002).
While cows may wade out to obtain better water, calves tend to only drink from the shore. By wading into surface sources, cattle pollute the water with their urine and feces and may disturb the water with their wading action. Eventually cattle may refuse to drink, and they will have to be moved even though local forage is still plentiful.
Calves require higher-quality water and will not fight cows or mud to obtain it. Increases of 50 pounds/head in weaning weight have been reported when water in sufficient quantity and quality is provided. Studies have shown that, when given a choice, cattle drank from a water trough 92% of the time rather than from a nearby stream (Bartlett, n.d.). Research also shows that yearling steer performance increased 23% when supplied with an alternate water source rather than dugouts (earthen dams or reservoirs). In addition to increased livestock and resource performance, by routing the livestock away from riparian zones, very large reductions (50–90%) in streptococci and coliform fecal organisms, waterborne diseases (foot rot, red nose, TB, mastitis, etc.), nitrogen, phosphorous, suspended solids, and surrounding erosion are realized. By pumping water to drinkers, ranchers can better utilize pastures, get superior animal growth and health, and provide higher-quality water (Pfost et al., 2007; Surber et al., n.d.).
Water Pumping Basics
Costs, reliability, and environmental concerns often influence a producer’s choice of surface water pumping system. When producers do not have economical access to grid electric power 3, they generally look to options such as ram, sling, diesel, wind (Figure 1), or solar powered pumps. When these choices are compared, solar pump systems are often the best choice due to the operational conditions inherent to New Mexico, which allows them to function effectively and economically (Foster et al., 2010).
Figure 1. Windmills are still a common source of power for off-the-grid water pumping systems.
Solar pumping systems for surface sources or wells can be portable, which is appealing because more and more producers want systems that can move among various locations. Some users are even powering broken windmill pump jacks with portable photovoltaic (PV) systems.
For pumping water from underground aquifers via wells, access to existing AC electric connections (closer than one-half kilometer or 0.3 mi) is again the best option. In remote locations, though, PV water pumping systems represent a very attractive, long-term, cost-effective alternative to hauling water, diesel pumps, and even traditional windmills for drinking water and many irrigation applications (drip/trickle, hose/basin, and some channel irrigation–although typically not for very high flow rates such as might be used in flood irrigation). The abundant and varied benefits of PV systems make them attractive in many situations.
A solar pumping system involves calculations and concepts that may make it difficult to determine a design if one is unfamiliar with the technology and terminologies. With this in mind, NMSU developed the following tools to aid and educate a potential user:
1. Two portable demonstration devices that illustrate the concepts and major system components for a solar pumping system. Each module is portable and therefore available for displays and presentations.
2. Literature and educational multimedia materials related to PV water pumping systems (https://www.youtube.com/playlist?list=PL89870B418A514D27), including comparisons between three main remote water pumping technologies (Table 1) used in New Mexico today, contrasting two different ways to mount PV modules (fixed-angle mounting vs. single-axis tracking systems), and a simple cost analysis for each of the three technologies and mounting systems (Foster et al., 2010).
>Table 1. Remote Water Pumping Technologies Comparison Chart | ||
Technology | Advantages | Disadvantages |
Solar |
Renewable/sustainable |
Variable water delivery depending on sun intensity |
No fuel costs |
Low flow rates |
|
Can be portable and remote |
Supplemental storage needed |
|
Very low operation/maintenance costs |
Extended time to meet required storage | |
Federal and state tax incentives |
Higher initial costs (although costs are trending lower) |
|
Acceptable capital costs and low recurring costs |
||
Reliable warranty of 20+ years for panels |
||
Relatively easy to install |
||
System is modular and may be modified to fit needs |
||
Wind | Renewable/sustainable | Only works when wind conditions are adequate |
No fuel costs | Winds are seasonal | |
Federal and state tax incentives | Some operating costs and higher repair/maintenance costs | |
Remote applications | Labor-intensive | |
Proven technology with pool of expertise and experience | Difficult to find parts and special tools needed | |
Lower initial costs | Low flow rates | |
Extended time to meet required storage | ||
High winds may damage windmill | ||
Fossil fuels (diesel) | Higher flow rate | Environmental issues |
Often no need for storage | Manually operated | |
Proven technology with large pool of expertise | Accessibility issues | |
Easy to install | Required periodic maintenance and replacement | |
Moderate to high initial cost | ||
Fuel costs and storage/transportation |
3. A Microsoft Excel spreadsheet to provide an easy and visual educational tool to present concepts behind PV technology and system design methodology (available to download at https://pubs.nmsu.edu/_circulars/CR671/CR671.xlsm ). This tool allows the user to follow the basic step-by-step design process, and offers sample components and simple economic analysis for a user-defined scenario. For the sake of organization and ease of use, the spreadsheet follows the design approach outlined in this publication. A companion publication, Circular 671, Designing Solar Water Pumping Systems for Livestock: User Manual (https://pubs.nmsu.edu/_circulars/CR671.pdf), covers the step-by-step instructions for using the Excel spreadsheet to design a solar water pump system.
Solar Water Pumping Systems
In order to design and successfully implement solar water pumping systems, you need an understanding of several concepts as well as information specific to how you will use your system. This includes:
- Daily water requirements and usage—drinking, irrigation, etc. Requirements for high volumes or flow rates may limit applications.
- Available sunlight, which depends on location. Low levels of sun may limit PV.
- Well characteristics, such as water depth, draw-down levels and recharge rates, seasonal variations, discharge elevation from earth’s surface to water discharge point, total feet of pipe, nominal diameter of the pipe, valves, and elbows, etc.
- Storage systems—catch tanks, concrete or plastic storage tanks, etc.—to ensure the daily water requirement is available during low-light conditions.
- Costs—capital, operation and maintenance, labor, life-cycle, etc.
- In addition, these factors should be considered:
- Who will install and maintain the system.
- Security—although ideal for remote locations, systems may be vulnerable to theft and vandalism.
- Environmental benefits (including low noise).
Basic Operation
With no moving parts, the PV panel takes energy from sunlight and generates DC electricity, which is then directed through a controller to the pump/motor in what is termed a “direct-coupled system” (Figure 2). The pump/motor combination (hereafter referred to as the pump) moves water from the source through a pipe to a discharge point, commonly a storage tank that feeds a trough-drinker (Figure 3). This direct-coupled system is intended to operate only during the day when sunlight is present, thus eliminating the expense and complexity of batteries 4. In a properly designed direct-coupled system, extra water must often be pumped into a storage tank. By providing storage, a producer can still provide their daily water requirements from the storage tank at night or on cloudy days. The amount of water pumped depends primarily on the amount of sunlight hitting the PV panels, the type of pump, and a few other factors. The amount of available sunlight is predictable by location, but there are always variations in weather (e.g., cloudy days 5). By using a simple direct-coupled approach, the operation, maintenance, costs, and complexity of the system are greatly reduced.
Figure 2. Direct-coupled solar pumping system. (Adapted from The University of Tennessee Extension.)
Components
Solar water pumping systems are composed of two primary components other than the well itself: the PV panels (or modules) and the pump.
PV Panels
PV panels are installed with mounting hardware that allows the panels to be oriented 6 to adjust the tilt of the modules to an optimum angle, elevate the modules for security, and minimize shading and damage (Figure 4). It is critical to minimize shading from structures and vegetation during all watering seasons because even partial shading can cause significant power loss. Locating modules close to the water source also helps minimize power losses and costs.
Modules are sized as DC power (watts [W]) and come in all sizes, from a few watts to over 250 W. Rated power is determined by the output voltage and current under standard sun intensity. A module rated at 50 W may have an operating voltage up to 17.4 volts (V) and a maximum current of 3.11 amps (A). Modules can be wired in series to increase output voltages and in parallel to increase current while also increasing total power. If sunlight changes (clouds), output current will fall and thus power will fall at a relative level (e.g., if sunlight is halved, current and power will be halved while voltage remains about the same). PV modules are sized and configured (series/parallel combinations) to power the second major component of the system: the pump.
Pumps
Pumps move water from wells or surface sources. It is important to analyze the system properly in order to make it as efficient and economical as possible while still meeting the watering requirements. Choosing and matching PV modules and pumps to meet the design constraints is vital. In designing an efficient system, one should minimize the amount of work required of the pump, which minimizes the amount of energy needed to operate the pump and thus the size and cost of components. By understanding these basic concepts beforehand, the designer will be able to determine the appropriate pump (and PV modules) for a system.
Figure 3. PV-powered pump systems often discharge to a storage tank to provide the daily water requirement even under lowlight conditions. (Photo from National Renewable Energy Labs, 1997.)
Figure 4. PV modules mounted to trailers can be easily oriented and moved based on water needs. (Photo from National Renewable Energy Labs, 1997.)
In selecting a pump, the following parameters should be considered:
- The required capacity or flow rate—how many gallons per minute (or per day) are needed.
- The conditions on the suction side of the pump (lots of grit, sand, or dissolved minerals in the water; algae growth; etc.).
- Whether the pump will be submersible in a well or pump from a surface source.
- The total head capability (how high can the pump move water).
- Space, weight, and position limitations, as well as cost of equipment and installation.
- Codes and standards, including the National Electrical Code (Wiles, 2001).
- The voltage(s) and power required for the pump and its working efficiency. 7
Once each parameter is clearly addressed, a pump can be selected. Pumps are classified as either positive-displacement or kinetic/centrifugal, and each has advantages. The list of available pumps (and manufacturers) is very extensive, and many will be capable of pumping from a surface source or a well. A pump for a “well application” is most commonly a DC submersible pump with a range of 12 V to more than 36 V, but may be much higher for very deep wells or high flow rates. The current is typically in the 3 to 5 A range, which equates to a rough operating power up to (though typically much less) around 1 horsepower (or 746 W). DC pumps use one-third to one-half the energy of AC pumps and are specifically designed to use solar power efficiently even during low-light conditions at reduced voltages without stalling or overheating. Solar pumps are low volume, pumping an average of 1 to 5 gallons per minute (gpm). A majority of pumps are positive displacement pumps (centrifugal-type pumps are also common), which enables them to maintain their lift capacity all through the solar day at varying speeds that result from changing light conditions 8. A good match between the pump, PV array, and system parameters is necessary to achieve efficient operation (Morris et al., 2002).
Other components that should be considered within the system are:
- Mounting system for the PV modules 9.
- A controller that allows the pump to start and operate under weak-sunlight periods (cloudy conditions, early morning, late afternoon).
- Water level sensor for on/off operation if using storage.
- Direct-burial wire (UF), grounding, disconnects,
and lightning protection. - Pipe, fittings, and other balance-of-system components (a common mistake is to oversize the piping).
- Most PV applications will be pumping at low flow rates (1–5 gpm), and these low flow rates will not have sufficient water velocity through a large pipe to keep suspended solids from settling out into the bottom of the piping.
- One-half- to two-inch piping is typically sufficient for most scenarios; smaller is cheaper and often more efficient.
Designing the System
A livestock watering well will be used in this example. This section will reference the accompanying Excel spreadsheet covered in Circular 671 (available to download at https://pubs.nmsu.edu/_circulars/CR671/CR671.xlsx). Italicized text (e.g., Daily Water Requirement) refers to sheets in the spreadsheet; sheets are accessed using the tabs at the bottom of the spreadsheet window.
Daily Water Requirement
The first step in a design is to determine the total amount of water needed per day. Many producers are used to thinking of pumping lots of water in a short time frame with large-capacity pumps. Solar pumping, like windmills, will pump water at slower flow rates (gpm) over a longer time.
To determine Daily Water Requirement using the spreadsheet tool, enter the quantity and type of animals (cow, horse, etc.) you wish to service from this well. These entries and Equation 1 are used to calculate total daily water required for each animal type (item).
Livestock’s daily water requirements vary with air temperature, the animal’s age and size, activity, distance to water, lactation, dry matter intake, and dry matter moisture content. Water needs closely correspond to quantity of feed or forage intake; as intake increases, the water requirement level will increase. However, with a moisture content of 70 to 90%, lush forage may supply a large amount of required moisture in cooler weather. Water consumption is almost directly proportional to the level of milk production, and lactating cows therefore need higher amounts of water. Air temperatures of 70 to 95°F may increase water requirements by 2.5 times (Pfost et al., 2007).
Common values of required gallons per day per animal in New Mexico can be found in the Daily Water Requirement spreadsheet tab or in Table 2, but you have the option to change these default values depending on your unique situation 10. The water demand should be estimated for the highest demand period (typically summer) and anticipated growth during the design cycle (at least 10 years). In windy, hot, dry areas, you should also take into account evaporation losses associated with open storage methods.
Once the total gallons/day/animal figure is calculated and any extra water requirements are entered, values are summed to yield the total daily water requirement in gallons/day. A multiplier may be added that can provide an extra water cushion, offset evaporation losses, or refill the storage tank.
Household water use demand is variable and depends on climate, usages, and other factors, but is typically around 75 gallons/person/day for drinking, cooking, and bathing. Irrigation water demand depends on local conditions, season, crops, methods of delivery, and evapotranspiration 11. Agriculture watering is usually greater in summer seasons when solar radiation is at its highest.
Table 2. Selected Example Amounts of Water Per Day for Various New Mexico Livestock
Items | Required amount of water per day gallons/day |
Nursing Cow | 17.5 |
Bred Dry Cows and Heifers | 14.5 |
Bulls | 19.0 |
Horses | 15.0 |
Sheep | 2.0 |
Humans | 75.0* |
*For drinking cooking, bathing, etc.
Storage Tank Capacity
Depending on climate and usage, storage tank capacity should equal 3 to 10 days of water use. For domestic use in a cloudy climate, 10 days may be necessary, while in sunny climates such as New Mexico, 3 days of storage for livestock watering may be sufficient. The storage tank size is calculated by multiplying the days-of-storage requirement by the daily water requirement and is provided as a reference only.
Solar Resource
Once the daily water requirement is calculated, the solar resource—“insolation,” or total sunlight reaching a specific location—is determined. Sunlight will provide the energy, via the PV modules, to run the pump, and sunlight value is determined by the nearest latitudinal coordinate of the well location (between 31 and 37° in New Mexico). When you insert this value, the spreadsheet determines the solar insolation for winter, summer, or a yearly average. It is recommended to use winter values since winter has the least amount of sunlight per day and it is best to design for the worst-case scenario. Nevertheless, you can choose to use the summer insolation value if you plan to water a summer-only pasture. A good rule of thumb is that the solar resource must be greater than 3.0 kWh/m2 per day (3,000 watt-hours per square meter of area in one day) for choosing a solar 12.
Pumping Requirements
Total dynamic head (TDH) is the total “equivalent” vertical distance that the pump must move the water, or the pressure the pump must overcome to move the water to a certain height. Water pressure is expressed in pounds per square inch (psi) and is defined as the force caused by the weight of water in a column of a certain height, also known as “head.” Head is a term relating feet of water in a column that exerts a certain pressure; for example, a column of water 10 ft high would exert 10 ft of head, or 4.3 psi (pressure). Knowing head, you can determine pressure and vice versa. Head is important to determine how hard the pump must work to move water from the source to a discharge point (i.e., to overcome the equivalent pressure of that water).
Static head is a major part of TDH and refers to the total vertical lift (distance) from the water level in the well to the discharge level. Static head is composed of the water depth in the well at its lowest seasonal and draw-down levels plus the elevation from the water surface to the discharge point 13. Entering these values, static head is calculated by Equation 2.
Pumps may be submersed in a well as deep as necessary to ensure reliable water supply (taking into account drawn-down levels, seasonal variations, and recharge rates). The water level variable in Equation 2 is measured from the water surface to the level of the water in the source—not the depth location of the pump. Placing the pump lower in the well (increasing its submergence) will NOT cause it to work harder or to pump less water, nor will it increase stress or wear on the pump. However, there are reasons to NOT set the pump too close to the bottom of the well:
1. A deep setting will increase cost, length, and weight of pipe and cable.
2. A setting near the bottom may increase the chance of sand or sediment being drawn into the pump and damaging the pump mechanism.
The pump must move the water from the well to an elevation, but it must also overcome friction losses in the system. These losses depend on the type of pipe (its roughness), total length of pipe including any horizontal runs, flow rate (speed) of the water in the pipe, fittings and joints, and pipe diameter. These friction losses, which are expressed in equivalent lengths of vertical pipe distance, are added to the static head to yield an equivalent TDH—i.e., what equivalent height would the pump need to move water given these values.
To determine friction losses in pipe, you should enter (in the Total Dynamic Head tab of the spreadsheet) the type of pipe (PVC, steel, etc.), total length of the pipe being used, and the nominal inside diameter of the pipe. The approximate head loss (HL) caused by friction within the pipe is calculated using the Hazen-Williams Empirical formula with assumptions of mediocre water temperature and somewhat turbulent pipe flow. The value generated is in units of “feet of head” (Mott, 2006). Equation 3 illustrates the Hazen-Williams formula.
The roughness coefficient variable C within the equation depends on the type of pipe, but the roughness coefficient is typically around 140. Q is the flow rate in gpm, D is the nominal inside diameter of the pipe in inches, and L is the total length in feet of the pipe for the system. Another standard “rule of thumb” is that friction losses in the pipe are typically 2–5% for a well-designed system.
The friction loss due to fittings must also be calculated. The friction losses for pipe fittings are converted to an equivalent length of pipe (in feet) and are a function of several variables. Losses due to fittings may be significant. To determine these losses, the spreadsheet lists many common fittings that might be utilized within the design of the system, and you should enter the quantity of each fitting used in your system. The equivalent friction loss for each fitting type is calculated using Equation 4. Table 3 shows a partial listing of some values used to calculate friction loss due to a fitting.
The equivalent head pipe friction loss values are calculated for each specific fitting used. These are then summed to give a total loss due to fittings (Mott, 2006).
TDH can now be calculated by using Equation 5.
Example of a TDH Calculation:
What is the TDH in a well with water depth of 150 ft (no draw-down) and flow rate of 4 gpm? The well is 80 ft from the storage tank, and the delivery pipe rises 8 ft to discharge into a tank. The piping is 0.75-in. diameter PVC, and there are three 90° elbows, one swing-type check value, and one gate-type valve in the pipe.
Solution: From Table 3, the three 90° elbows add the equivalent of 5.625 ft of pipe, the check valve 8.4375 ft, and the gate valve 0.56 ft, giving a total equivalent pipe length head of 14.6 ft (rounded to the nearest hundredth) due to fittings losses. The total length of pipe is 150 (well water depth) + 80 (distance from well to storage tank) + 8 (distance from surface discharge to tank) = 238 ft. From the HL calculation (Equation 3), 100 ft of 0.75-in. pipe at 4 gpm has a pressure drop of 4.9 ft/100 ft of tube, which yields 4.9 × 238 / 100 = ~11.74 ft.
Table 3. Examples of Equivalent Length in Pipe Diameter (L/d) of Sample Pipe Fittings
Pipe Fitting | L/d (inches) |
Globe valve, fully open | 275 |
Gate valve, fully open | 9 |
90° standard elbow | 30 |
Swing check valve | 135 |
Standard tee, flow through branch | 60 |
The water must be lifted 150 + 8 = 158 ft (static head); therefore, TDH (Equation 5) is 158 + 11.74 + 14.6 = ~184 ft.
Hydraulic Workload
Oftentimes, we may work in units other than gallons and feet. One U.S. gallon is equal to about 0.0037854 cubic meters, while 1 foot of distance is equal to about 0.3048 meters. If we convert TDH from feet to meters and the daily water volume from gallons to cubic meters, then we can calculate something called the hydraulic workload (Equation 6), which is an excellent indication of the power that will be required to meet the designed system constraints.
If the hydraulic workload is less than 1,500 m4, then the project is a good candidate for solar PV. If it is between 1,500 and 2,000 m4, it will be borderline. If the hydraulic workload is greater than 2,000 m4, you may need to consider other options.
Pump and Flow Rate
The flow rate (gpm) is the volume of water that is pumped in a set time period and is determined via Equation 7.
In the Pump Selection tab of the spreadsheet, you are shown the calculated Q and TDH. Using these two key values, you must manually choose a specific pump (from an initial limited selection) that will be capable of pumping water at the necessary Q and TDH. Once a pump is selected, we determine at what voltage this pump will operate (12 V, 30 V, etc.) and how much power (watts) is required to run this pump assuming standard pump efficiency (η ~35%). This is the power that de-rated 14 PV modules must supply to operate the pump. Pump power can often be looked up in pump tables, but it can also be determined by Equation 8.
PV Determination
The Array Sizing spreadsheet tab involves the automatic sizing of the PV array given the calculated and manually selected pump parameters. The first calculation performed is to determine the number of PV modules in series—a string. Each PV module has an operating output current and voltage. Connecting modules in series increases the total voltage to match or exceed the required pump motor voltage (determined earlier). Equation 9 illustrates this, while Equation 10 describes how the PV strings may be connected in parallel to increase total current and thus total power to match or exceed the required pump’s power (also determined earlier). Voltage multiplied by current determines total power provided by the PV array in watts (or converted to horsepower, HP). NOTE: It is possible that there will only need to be a single module or modules only in series and not in parallel.
In Equation 9, the 17.4 V value represents the operational voltage for our PV module
In Equation 10, the 3.11 A represents the PV panel’s rated current (at standard operating conditions) and the 0.80 value represents the de-rating factor.
NOTE: These values are for a pre-selected example PV module. If other size PV modules are selected, then the values must be changed to reflect those modules’ voltage and current.
Because we round up the number of strings and parallel combinations to whole numbers, the total amount of energy and therefore water pumped will be greater than our daily requirements on any full sunny day. This is typically not an issue when float switches are incorporated into storage systems, which will stop the pumping when the tank is full. Excess power produced by solar panels can be used for cathode protection, to aerate a dugout, or to power an electric fence.
The estimated total daily water pumped (gallons/day) on a full sunny day can be found by Equation 11:
Final Design Specifications
The Design Specification spreadsheet tab summarizes the design values obtained through the use of the spreadsheet and lists the key components and materials for this scenario’s direct-coupled solar water pumping system. The description and quantities for specific items are obtained from calculations or specified by you. The cost for each itemized component is calculated by multiplying the quantity of each item by a representative retail price, but prices will of course vary over time. The necessary length of UF wire is roughly determined by the length of pipe plus an extra 25%. The market price for the UF wire is for 250-ft rolls. Pipe is assumed to be PVC and the price is calculated by dividing the total length of needed pipe by 10 (PVC pipe is typically sold in 10-ft lengths) and multiplying by its market price. The grand total of the entire system (not including the well, labor, storage, etc.) is calculated by adding up all the itemized totals. This will reflect an approximate cost to construct the system plus the costs of other materials, labor, sales taxes, shipping, etc. Federal and state tax incentives may lower the initial costs by up to 40% (as of 2012).
Conclusion
Using the spreadsheet allows you to test various design scenarios and demonstrate the design method and terminology for a direct-coupled solar water pumping system. It is important to consider the limits of this spreadsheet because it is only able to calculate for flow rates up to ~4 gpm and TDH values no greater than ~230 ft due to the very limited PV and pump selection options within this version. In the case of design values outside these limits or for pumps or PV module choices not available within the spreadsheet, you should reference alternative performance data provided by other pump or PV manufacturers. We hope that later versions of this spreadsheet will address several of these issues.
Photovoltaic-powered water pumping systems are attractive for livestock and agricultural producers with remote water sources and limited access to AC power. Even though wind has been in use for decades and will continue to provide effective solutions for water pumping, solar power has made significant steps toward becoming the system of choice for these situations. Solar systems’ low maintenance and simple operation, lack of fuel (transportation or storage) costs, environmental friendliness, and competitive life-cycle economics place them at the forefront of choices for supplying water to livestock or agriculture. The technology for solar water pumping is exceeding all expectations, and will continue to be a viable choice for more and more users as its capabilities, reliability, and versatility increase while costs decrease.
The spreadsheet, documentation, and demonstration modules provide you with terminologies, knowledge, and skill sets that can be the foundation for informed choices relating to alternative water pumping systems. For additional information, contact your county
Cooperative Extension agent or NMSU.
Acknowledgments
The author wishes to express extreme gratitude for the assistance of the following:
College of Engineering and Engineering NM: https://engr.nmsu.edu/index.shtml
NMSU Cooperative Extension Service: https://extension.nmsu.edu/
New Mexico Space Grant Consortium: https://www.nmspacegrant.com/
Southwest Technology Development Institute:
Department of Engineering Technology and Surveying Engineering: https://et.nmsu.edu/
References
Bartlett, B. n.d. Watering systems for grazing livestock [Online]. CR670
Boyle, G. 2004. Renewable energy. Oxford: Oxford University Press.
Buschermohle, M., and R. Burns. n.d. Solar-powered livestock watering systems [Online]. Available from https://utextension.tennessee.edu/publications/documents/pb1640.pdf
Foster, R., and A. Ellis. 2003. Renewable energy for water pumping applications in rural villages [Online; NREL/SR-500-30361]. Available from https://www.nrel.gov/docs/fy03osti/30361.pdf
Foster, R., M. Ghassemi, and A. Cota. 2010. Solar energy: Renewable energy and the environment. Boca Raton, FL: Taylor & Francis Group.
Masters, G.M. 2004. Renewable and efficient electric power systems. Hoboken, NJ: John Wiley & Sons, Inc.
Morris, M., and V. Lynne. 2002. Solar-powered livestock watering system [Online]. Available from https://www.clemson.edu/sustainableag/IP217_solar_livestock_watering.pdf
Mott, R.L. 2006. Applied fluid mechanics (6 ed.). Upper Saddle River, NJ: Pearson Prentice Hall.
National Renewable Energy Labs. 1997. Electricity when and where you need it: From the sun: Photovoltaics for farms and ranches [Online; NREL/BR-412-21732]. Available from https://www.nrel.gov/docs/gen/fy97/21732.pdf
Pfost, D., J. Gerrish, M. Davis, and M. Kennedy. 2007. Pumps and watering systems for managed beef grazing [Online]. Available from https://extension.missouri.edu/p/EQ380
Surber, G., K. Williams, and M. Manoukian. n.d. Drinking water quality for beef cattle: An environment friendly & production management enhancement technique [Online].
Wiles, J. 2001. Photovoltaic power systems and the National Electrical Code: Suggested practices [SAND87-0804]. Albuquerque, NM: Sandia National Laboratories.
Footnotes
1An excellent source on windmills: https://aces.nmsu.edu/ces/windmill
2It has been shown that livestock will only travel a limited distance to water sources with typical water source spacing of one source per 250 ha to harvest grasslands, otherwise there is strong potential for overgrazing close to water supplies.
3It can cost $10,000 to $30,000 per mile to install electrical power line through rugged terrain.
4Batteries are expensive, must be replaced every few years, and require periodic maintenance, while the useful life of storage tanks may be decades.
5PV panels may produce up to 80% of their maximum output power on partly cloudy days, and even on extremely overcast days can still produce about 25%
of their maximum.
6As a rule of thumb, PV panels are faced due south and at a tilted angle equal to the location’s latitude. This may be fixed or variable depending on seasonal conditions and other factors. For example, a summer tilt angle would be flatter to capture more sun with tilt angle equal to the latitude angle -15° while a winter tilt angle might be latitude angle +15°. In Las Cruces, the latitude angle would be 32° tilt, a summer tilt of 17°, and a winter tilt of 47°.
7Average pump efficiencies are in the 25–35% range.
8See Foster et al. (2010) for a more complete pump and PV discussion.9PV mounts may be fixed racks or poles, or some type of tracking system that follows the sun.
10See your NMSU county Extension agent for more information.
11Contact your county Extension agent for information on estimated evapotranspiration rates for your area.
12 All areas of New Mexico meet this limit with values well above 5 kWh/m2 per day. New Mexico climate website (https://weather.nmsu.edu) has good historical solar, wind, and temperature data.
13Draw-down is the level of water that may drop in the well as pumping occurs—the well pipe is refilled at a recharge rate. The low flow rates of solar systems have less negative impact on draw-down.
14De-rating takes into account temperature and soiling effects on the modules.
Disclaimer: This document is intended for educational purposes only in providing a basic understanding of terminology and concepts of design. It is not intended to be used beyond this purpose. The authors incorporated good analysis, but all situations are different and you should consult a professional in all cases.
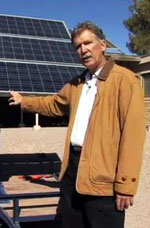
Thomas Jenkins has been a professor in NMSU's Department of Engineering Technology and Survey Engineering since 1990. He previously worked for many years in both private and public sectors as a computer scientist and engineer. Professor Jenkins lead the effort to develop the College of Engineering Renewable Energy Technology minor and helped establish the NMSU student organization Engineers Without Borders.
Contents of publications may be freely reproduced for educational purposes. All other rights reserved. For permission to use publications for other purposes, contact pubs@nmsu.edu or the authors listed on the publication.
To find more resources for your business, home, or family, visit the College of Agricultural, Consumer and Environmental Sciences on the World Wide Web at pubs.nmsu.edu
New Mexico State University is an equal opportunity/affirmative action employer and educator. NMSU and the U.S. Department of Agriculture cooperating.
December 2014, Las Cruces, NM